At present, there are a wide variety of sensors on the market that are dazzling. But for medical system OEMs, choosing the best pressure sensor for a medical device that is in a liquid-sensing or condensing-humid application is not an easy task. Designers need to choose sensors that achieve a good balance between technical functionality, reliability, and the cost of a specific application.
For applications that require compatibility with liquid media, medical device designers have traditionally had little choice. Before the liquid-compatible board-mounted sensors were available on the market, the only choice for designers was a dielectrically isolated pressure sensor. Nowadays, when dealing with higher pressures (eg, pressures above 150 psi), we still choose media-isolated pressure sensors; for lower pressures, these sensors are too large compared to board-mounted sensors. The price is too expensive.
What is the best choice if the application environment is at medium intensity and the sensor must be in contact with a liquid or humid gas in a Class C application?
Class C applications include gas/liquid chromatographs, chemical analyzers, and blood diagnostic equipment. The key requirement for these devices is to accurately measure the pressure of reagents, samples, and cleaning fluids. According to the given pressure range (usually less than 150psi) and size restrictions, board mounted pressure sensors are preferred.
Designers often choose to place the sensor as close as possible to the medium to be measured in order to obtain the most accurate readings. However, if the pressure sensor is incompatible with the liquid to be measured, this will cause great trouble for the medical device designer, forcing them to add protection functions for the sensor. In many cases, these additional components can significantly increase the design time and cost of medical devices.
Even in diagnostic applications where the fluid does not normally touch the sensor, the designer still needs to consider the worst case, such as the possibility of overpressure in the application or the fluid flowing in the tube beyond a preset value to touch the sensor.
What can a designer do to ensure that the sensor is isolated from the fluid? This involves the design of the piping, so they need to consider the positioning of the components in the system to isolate the fluid from the sensors, or to add additional components such as filters in the design to solve the problem of humidity.
In order to simplify the designer's selection of suitable pressure sensor workloads for medical devices, sensor manufacturers have specifically developed targeted solutions. These solutions not only isolate the liquid medium, but also eliminate the need to integrate additional protection features, allowing engineers to ensure that liquids and sensors do not touch without modifying the design, simplifying design work.
A chemical analyzer is a very convincing application example. The analyzer uses a liquid medium compatible board mounted pressure sensor. In a chemical analyzer, a pipette is used to draw the sample liquid and the sample is dropped into a sample bottle for mixing or analysis. At this point, it should be judged whether the pipette is unblocked or correctly placed in the sample bottle to ensure the correct amount of liquid, which requires the use of a pressure sensor.
The most basic requirement of a chemical analyzer application is to accurately measure the specific amount of liquid flowing through the system in a repeatable manner. Therefore, the pressure sensor must have high accuracy and repeatability, be capable of low-pressure work requirements, and be able to withstand the due to flushing. Or the higher pressure generated by cleaning the liquid passage.
24PC/26PC board mounted pressure sensors from Honeywell Sensing and Control deliver high resolution and repeatability, detect small pressure changes and provide readings, and accurately measure flow in a repeatable manner The specific amount of liquid through the system ensures that the liquid has a flow rate and a flow rate (this is a key point for the operation of the analytical device).
In addition, Honeywell's 24PC/26PC sensor is a unique solution for applications that require both pressure ports of the differential sensor to contact the fluid.
In ventilator applications, pressure sensors are used to measure the patient's inhaled and exhaled airstreams, and therefore require highly stable and highly accurate measurement requirements in order to accurately measure air and oxygen pressures and prevent them from exceeding setpoints. Honeywell's HSC/SSCTrustability sensors have extremely stringent accuracy and can detect pressures down to 250 Pa (1 in. water column) and are perfect for this application. In addition, the sensor also supports I2C or SPI digital outputs that interface directly with microprocessors and microcontrollers, simplifying design and improving performance.
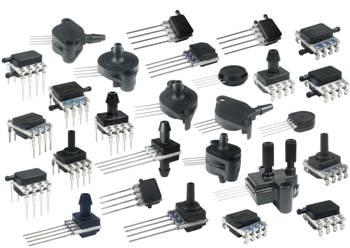
The TruStability HSC/SSC Series pressure sensors are equipped with a range of liquid media options for stable operation in direct contact with liquid media or condensation environments. These options are a key consideration when placing the sensor close to the patient, especially in the exhalation part of the ventilator, which must tolerate high humidity air caused by the patient's coughing and exhalation.
The 24PC/26PC and TruStability HSC/SSC pressure sensors can be placed directly in the media path of a chemical analyzer, ventilator, blood analyzer, or other similar type of medical device for optimal pressure readings. In addition, the sensor is equipped with a large number of selectable modes that offer not only extremely high flexibility, but also a variety of other features such as pressure range, package type, and digital/analog output range. All sensors can withstand a variety of non-corrosive, deionized liquid or gas applications.
Selecting a pressure sensor In the design of medical device applications, it is critical that designers need to understand which types of fluids will be in contact with the pressure sensor in order to select the appropriate sensing solution that is compatible with the specific fluid. They also need to further understand other key design criteria such as pressure type and range, accuracy, supply voltage, packaging requirements, and output type.
For practical purposes, designers should consider pressure sensors that are compatible with liquid media and have full compensation, amplification, and calibration features. Such sensors can provide amplified signals and avoid the need to design signal conditioning components on the printed circuit board, thereby providing benefits such as space saving, reliable performance, lower cost, and shorter design time.
Of course, the best choice should be determined first according to the application. For example, in an alarm circuit or other applications, the designer may prefer a low-cost pressure sensor that is compatible with the liquid medium but has no amplification and compensation characteristics.
At the same time, pressure sensors that are easy to integrate into the design should be found. This means that the device should provide multiple port type, package, and output type (analog and digital) options. In addition, the pre-test of the sensor is also a great advantage to improve the development and production cycle.
For applications that require compatibility with liquid media, medical device designers have traditionally had little choice. Before the liquid-compatible board-mounted sensors were available on the market, the only choice for designers was a dielectrically isolated pressure sensor. Nowadays, when dealing with higher pressures (eg, pressures above 150 psi), we still choose media-isolated pressure sensors; for lower pressures, these sensors are too large compared to board-mounted sensors. The price is too expensive.
What is the best choice if the application environment is at medium intensity and the sensor must be in contact with a liquid or humid gas in a Class C application?
Class C applications include gas/liquid chromatographs, chemical analyzers, and blood diagnostic equipment. The key requirement for these devices is to accurately measure the pressure of reagents, samples, and cleaning fluids. According to the given pressure range (usually less than 150psi) and size restrictions, board mounted pressure sensors are preferred.
Designers often choose to place the sensor as close as possible to the medium to be measured in order to obtain the most accurate readings. However, if the pressure sensor is incompatible with the liquid to be measured, this will cause great trouble for the medical device designer, forcing them to add protection functions for the sensor. In many cases, these additional components can significantly increase the design time and cost of medical devices.
Even in diagnostic applications where the fluid does not normally touch the sensor, the designer still needs to consider the worst case, such as the possibility of overpressure in the application or the fluid flowing in the tube beyond a preset value to touch the sensor.
What can a designer do to ensure that the sensor is isolated from the fluid? This involves the design of the piping, so they need to consider the positioning of the components in the system to isolate the fluid from the sensors, or to add additional components such as filters in the design to solve the problem of humidity.
In order to simplify the designer's selection of suitable pressure sensor workloads for medical devices, sensor manufacturers have specifically developed targeted solutions. These solutions not only isolate the liquid medium, but also eliminate the need to integrate additional protection features, allowing engineers to ensure that liquids and sensors do not touch without modifying the design, simplifying design work.
A chemical analyzer is a very convincing application example. The analyzer uses a liquid medium compatible board mounted pressure sensor. In a chemical analyzer, a pipette is used to draw the sample liquid and the sample is dropped into a sample bottle for mixing or analysis. At this point, it should be judged whether the pipette is unblocked or correctly placed in the sample bottle to ensure the correct amount of liquid, which requires the use of a pressure sensor.
The most basic requirement of a chemical analyzer application is to accurately measure the specific amount of liquid flowing through the system in a repeatable manner. Therefore, the pressure sensor must have high accuracy and repeatability, be capable of low-pressure work requirements, and be able to withstand the due to flushing. Or the higher pressure generated by cleaning the liquid passage.
24PC/26PC board mounted pressure sensors from Honeywell Sensing and Control deliver high resolution and repeatability, detect small pressure changes and provide readings, and accurately measure flow in a repeatable manner The specific amount of liquid through the system ensures that the liquid has a flow rate and a flow rate (this is a key point for the operation of the analytical device).
In addition, Honeywell's 24PC/26PC sensor is a unique solution for applications that require both pressure ports of the differential sensor to contact the fluid.
In ventilator applications, pressure sensors are used to measure the patient's inhaled and exhaled airstreams, and therefore require highly stable and highly accurate measurement requirements in order to accurately measure air and oxygen pressures and prevent them from exceeding setpoints. Honeywell's HSC/SSCTrustability sensors have extremely stringent accuracy and can detect pressures down to 250 Pa (1 in. water column) and are perfect for this application. In addition, the sensor also supports I2C or SPI digital outputs that interface directly with microprocessors and microcontrollers, simplifying design and improving performance.
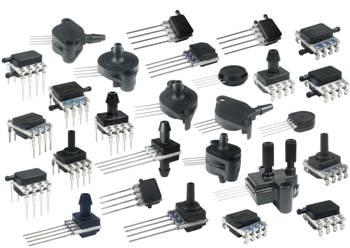
Honeywell's TruStability pressure sensor series has a wide range of configurations, making design and development easy.
The TruStability HSC/SSC Series pressure sensors are equipped with a range of liquid media options for stable operation in direct contact with liquid media or condensation environments. These options are a key consideration when placing the sensor close to the patient, especially in the exhalation part of the ventilator, which must tolerate high humidity air caused by the patient's coughing and exhalation.
The 24PC/26PC and TruStability HSC/SSC pressure sensors can be placed directly in the media path of a chemical analyzer, ventilator, blood analyzer, or other similar type of medical device for optimal pressure readings. In addition, the sensor is equipped with a large number of selectable modes that offer not only extremely high flexibility, but also a variety of other features such as pressure range, package type, and digital/analog output range. All sensors can withstand a variety of non-corrosive, deionized liquid or gas applications.
Selecting a pressure sensor In the design of medical device applications, it is critical that designers need to understand which types of fluids will be in contact with the pressure sensor in order to select the appropriate sensing solution that is compatible with the specific fluid. They also need to further understand other key design criteria such as pressure type and range, accuracy, supply voltage, packaging requirements, and output type.
For practical purposes, designers should consider pressure sensors that are compatible with liquid media and have full compensation, amplification, and calibration features. Such sensors can provide amplified signals and avoid the need to design signal conditioning components on the printed circuit board, thereby providing benefits such as space saving, reliable performance, lower cost, and shorter design time.
Of course, the best choice should be determined first according to the application. For example, in an alarm circuit or other applications, the designer may prefer a low-cost pressure sensor that is compatible with the liquid medium but has no amplification and compensation characteristics.
At the same time, pressure sensors that are easy to integrate into the design should be found. This means that the device should provide multiple port type, package, and output type (analog and digital) options. In addition, the pre-test of the sensor is also a great advantage to improve the development and production cycle.