Self-operated pressure regulating valve works
Self-operated pressure regulators are divided into three series: self-operated pressure, differential pressure and flow control valves. Self-operated pressure regulating valve is divided into two categories before and after the valve according to the pressure point. When the pressure point is in front of the valve, it is used to adjust the pressure constant before the valve; when the pressure point is behind the valve, it is used to regulate the pressure after the valve is constant. .
Self-operated pressure regulators are divided into three series: self-operated pressure, differential pressure and flow control valves. Self-operated pressure regulating valve is divided into two categories before and after the valve according to the pressure point. When the pressure point is in front of the valve, it is used to adjust the pressure constant before the valve; when the pressure point is behind the valve, it is used to regulate the pressure after the valve is constant. . When the front valve pressure and the rear valve pressure are simultaneously introduced into both sides of the air chamber of the actuator, the self-operated differential pressure regulating valve can adjust the pressure at both ends of the regulating valve to be constant, and can also introduce the pressure difference installed at both ends of the orifice plate of the pipeline into the membrane to execute. On both sides of the air chamber of the mechanism, a self-operated flow control valve is formed, or the flow rate is adjusted by a self-operated differential pressure regulating valve after the flow is detected in other ways.
Valve pressure control
After the pre-valve pressure P1 of the working medium is throttled by the valve body and the valve seat, it becomes the post-valve pressure P2. P2 is input into the lower membrane chamber of the actuator through the control line and acts on the top plate. The generated force balances with the reaction force of the spring, determines the relative position of the valve core and the valve seat, and controls the pressure behind the valve. When the pressure P2 increases, the force acting on the top plate by P2 also increases. At this time, the force of the top plate is greater than the reaction force of the spring, so that the valve core is closed to the position of the valve seat until the force of the top plate and the reaction force of the spring are balanced. At this time, the flow area of ​​the valve plug and the valve seat decreases, and the flow resistance increases, thereby lowering P2 to a set value. Similarly, when the post-valve pressure P2 decreases, the direction of action is opposite to that described above. This is the principle of the self-operating (after-valve) pressure regulating valve. This type of valve should generally be installed horizontally in the pipeline.
Pre-valve pressure control
After the pre-valve pressure P1 of the working medium is throttled by the valve body and the valve seat, it becomes the post-valve pressure P2. At the same time, P1 is input into the upper membrane chamber of the actuator through the control pipeline and acts on the top plate. The generated force balances with the reaction force of the spring, determines the relative position of the valve core and the valve seat, and controls the pressure before the valve. When the pressure P1 increases, the force acting on the top plate by P1 also increases. At this time, the force of the top plate is greater than the reaction force of the spring, so that the valve core moves away from the valve seat until the force of the top plate balances with the reaction force of the spring. At this time, the flow area of ​​the valve plug and the valve seat is reduced, and the flow resistance becomes smaller, so that P1 is reduced to a set value. Similarly, when the pressure behind the valve P1 decreases, the direction of action is opposite to the above, which is the working principle of the self-operating (pre-valve) pressure regulating valve.
Self-operated temperature control valve working principle (heated type)
The temperature control valve works according to the principle of incompressible and thermal expansion and contraction of the liquid. Heating self-operated temperature control valve, when the temperature of the controlled object is lower than the set temperature, the liquid in the warm package shrinks, the force acting on the actuator push rod decreases, and the valve core component opens the valve under the action of the spring force Increase the flow of heating medium such as steam and hot oil to increase the temperature of the controlled object. When the temperature of the controlled object reaches the set value, the valve closes. After the valve is closed, the temperature of the controlled object drops, the valve opens again, and the heating medium Into the heat exchanger, the temperature rises again, so that the temperature of the controlled object is a constant value. The valve opening size is related to the difference between the actual temperature of the controlled object and the set temperature.
Self-operated temperature control valve working principle (cooling type)
The working principle of the self-operated thermostatic valve for cooling can refer to the self-operated thermostatic valve for heating, except that when the valve core part is opened and closed under the action of the actuator and the spring force, the valve body passes through the cold medium and is mainly applied to it. Temperature control in the cooling device.
Self-operating flow regulating valve works
After the controlled medium enters the valve, the pressure before the valve P1 is input into the lower chamber through the control line, and the pressure Ps after throttling the throttle valve is input into the upper chamber. The difference between P1 and Ps is ΔPs=P1-Ps and is called the effective pressure. . The thrust generated by P1 acting on the diaphragm and the thrust produced by Ps acting on the diaphragm balance with the spring reaction force to determine the relative position of the valve plug and the valve seat, thereby determining the flow through the valve. When the flow through the valve increases, that is, △Ps increases. As a result, P1 and Ps respectively act on the lower and upper film chambers to move the spool toward the valve seat, thereby changing the flow area between the valve plug and the valve seat. As Ps increases, the thrust of the increased Ps acting on the diaphragm plus the spring reaction force and the thrust of P1 acting on the diaphragm are balanced at the new position to achieve the purpose of controlling the flow. On the contrary, the same reason.
Self-regulating valve is used to adjust the process parameters such as medium flow, pressure, temperature and liquid level in the field of industrial automation process control. According to the control signal in the automation system, the opening degree of the valve is automatically adjusted so as to adjust the flow, pressure, temperature and liquid level of the medium.
Self-operated pressure regulating valve main features and technical parameters
main feature
1. The self-operated pressure regulating valve does not need external energy and can work in an environment without electricity and air, which is convenient and energy-saving.
2. The pressure ranges are fine and cross each other, with high adjustment accuracy.
3, the pressure set value can be set continuously during operation.
4, after the valve pressure adjustment, the ratio between the pressure before the valve and the pressure behind the valve is 10:1~10:8
5, rubber diaphragm type testing, the implementation of high-precision detection agencies, sensitive action.
6, the use of pressure balance mechanism, make the valve responsive and accurate control.
Technical Parameters
Nominal diameter: DN15, 20, 25, 32, 40, 50, 65, 80, 100, 125, 150, 200, 250mm
Nominal pressure: PN1.0, 1.6, 4.0, 6.4 MPa
Flange standard: ANSI, JIS, DIN, GB, JB (Special according to user)
Body material: cast steel (ZG230-450), cast stainless steel (ZG1Cr18Ni9Ti, ZG1Cr18Ni12Mo2Ti)
Spool material: hard seal - stainless steel (1Cr18Ni9Ti, 1Cr18Ni12Mo2Ti); soft seal - stainless steel inlaid rubber ring
Pressure balance: stainless steel bellows (DN15 ~ 125), balanced diaphragm (DN150 ~ 250)
The main technical parameters and performance indicators
Compression type: used for valve pressure adjustment, when the valve pressure increases, the valve closes, in order to achieve the purpose of decompression, voltage regulation.
Pressure open type: used for valve pressure adjustment, when the valve pressure increases, the valve opens to achieve the purpose of pressure relief, voltage regulation.
Technical indicators and uses
Direct-acting self-operated pressure regulating valve is used in the absence of electricity, no gas, using the pressure of the controlled medium itself to change the control valve (K type) or valve (B type) pressure constant pressure or decompression, with a condenser , It can be continuously used under the steam of 350 degrees Celsius, the film type is used for the pressure less than or equal to 0.7MPa, the piston type is used for the pressure of 0.7-2.5MPa, widely used in petroleum, chemical industry, electric power, metallurgy, food, textile and other industries The gas, liquid, and steam in the equipment are decompressed, pressure relief, and pressure regulation.
Features
The self-operated pressure regulating valve can work in a place without electricity or air without external energy, which is convenient and saves energy. The pressure ranges are fine and intersect with each other, and the adjustment accuracy is high. The pressure setting can be set continuously during operation. For the pressure adjustment after the valve, the ratio of the pressure before the valve to the pressure behind the valve may be 10:1 to 10:8. Diaphragm type detection, high accuracy of the actuator and sensitive operation. The pressure balance mechanism makes the control valve responsive and accurate.
Shanghai Lugong Valve Industry Co., Ltd. (Lugong LUG)
Standard Water Chiller easy to be iced and freezed during running when the ambient temperature is below 0℃. Glycol Water Chiller will solve the problem with adding anti-freezing liquid. Widely used in milk industriy, beverage factory and beer industriy etc.
characterisitcs:
1. Cooling capacity: 8kW-200kW
2. The Industrial Water Chiller widely used in the low temperature 0℃ to -20℃ and running reliable.
3. With environment friendly R404A refrigerant.
4. Structure: Panels and base frame are made from galvanized steel protected with polyester powder painting to ensure total resistance to atmospheric agents.
5. Compressor: Hermetic scroll type compressor, equipped with the crankcase heater and thermal protection with thermal overload cut-out and crankcase heater mounted on rubber vibration isolators.
6. Water circuit: Built with air vent valve, water drain connection, and female-threaded hydraulic connectors. Water pump (8kW-30kW), differential pressure switch, Expansion tank (8kW-30kW).
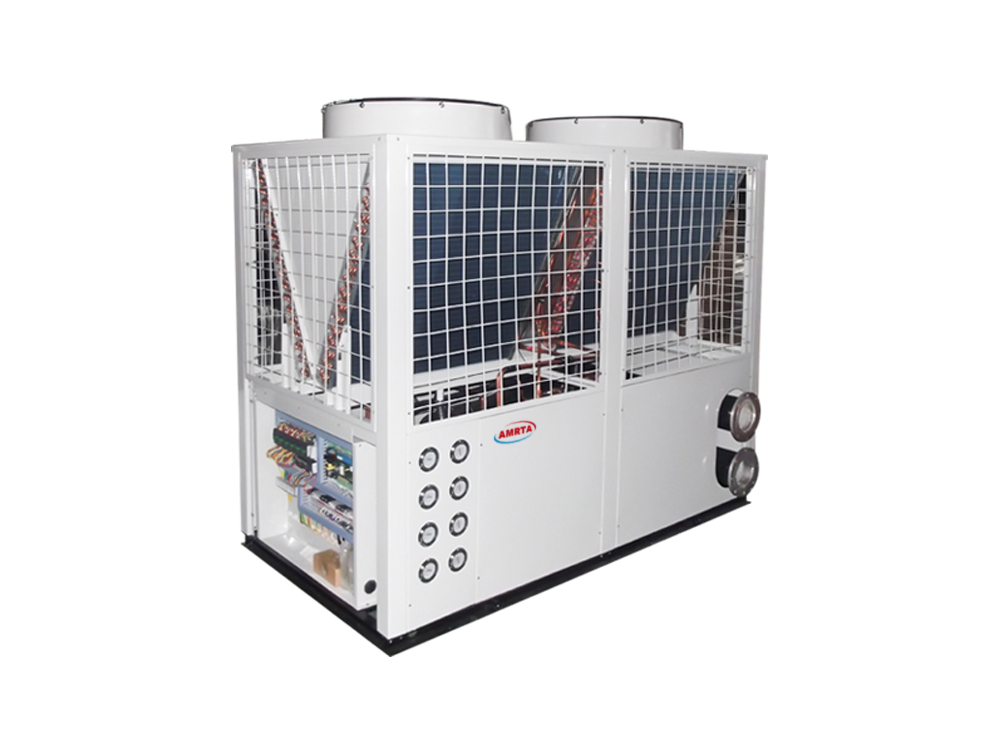
Glycol Water Chiller
Glycol Water Chiller,Industrial Glycol Water Chiller,Ethylene Glycol Water Chiller,Low Temperature Glycol Water Chiller
Jinan Amrta Air Conditioning Co.,Ltd , https://www.waterchiller.pl