Understanding the Differences Between Oxyfuel Cutting and Plasma Cutting: Choosing the Best Option for Your Needs
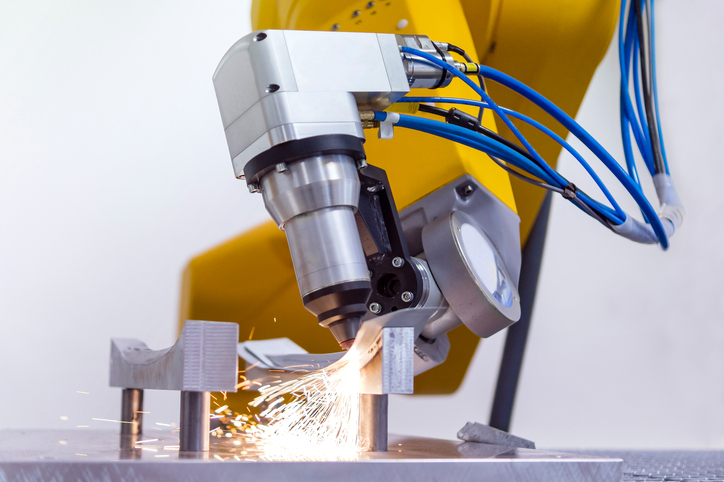
When it comes to automation in modern manufacturing, robotic cutting is a common and efficient solution. However, choosing between robotic oxyfuel cutting and robotic plasma cutting can be challenging. Both technologies have their own strengths and limitations, making them suitable for different applications.
Understanding the differences between these two methods is crucial for selecting the right one for your specific needs. Whether you're working with thick steel plates or thin aluminum sheets, the choice of cutting technology can significantly impact productivity, cost, and quality.
How Plasma Cutting and Oxyfuel Cutting Work
Plasma cutting uses an electric arc to ionize a gas, typically compressed air, creating a high-temperature plasma stream that melts the material. This method is fast and precise, especially for thinner materials. The plasma torch delivers a concentrated heat source that allows for quick cuts with minimal distortion.
Oxyfuel cutting, on the other hand, relies on a mixture of oxygen and fuel gas to create a high-temperature flame. The material is first preheated to its ignition point, and then a high-pressure oxygen jet is used to oxidize and cut through the metal. This process is ideal for thicker metals but slower compared to plasma cutting.
Pros and Cons of Each Technology
Plasma cutting is known for its speed and versatility, particularly when working with non-ferrous metals like aluminum and copper. It offers clean cuts and is well-suited for automated systems. However, it may not be as effective for very thick or ferrous materials.
Oxyfuel cutting excels when dealing with thick iron-based materials. It provides excellent control and precision, making it a preferred choice for heavy-duty applications. However, it is generally slower and less efficient for thin materials, and requires more setup time.
Both technologies have their place in the manufacturing world. The decision between oxyfuel and plasma cutting depends on factors such as material type, thickness, desired cut quality, and production speed. In some cases, a combination of both methods may be the most efficient approach.
Choosing the right cutting technology can make a big difference in your workflow. By understanding the strengths and limitations of each, you can make an informed decision that aligns with your operational goals.
If you're looking for reliable robotic cutting solutions, consider exploring advanced systems from industry leaders like Genesis Systems Group, which offer both oxyfuel and plasma cutting options tailored to various industrial needs.
Posted in Robotic ApplicationsSmall Raymond Mill,also called high pressure roller mill, fine power grinding mill, stone ginding mill machine. The grinding mill machine includes Ball Mill, raymond mill, Wet Pan Mill and rod mill machine. They are applicable to the grinding and processing of more than 280 kinds of non-flammable and non-explosive materials with hardness less than 7 and humidity less than 6% in mining, construction, chemical industry and metallurgy, such as barite, calcite, feldspar, talcum, marble, limestone, clay, glass. The fineness of the finished product can be adjusted from 100 mesh to 325 mesh according to requirements.
While the ball mill can divide into 2 types, wet ball mill and dry ball mill. Ball mill is a mineral processing machine for milling the materials into powders after they are crushed. It is widely applied to the production of cements, silicate products, building materials, fireproof materials, fertilizers, glass, ceramics as well as nonferrous and ferrous metal processing industries.
Stone Grinding Mill Machine,Gold Ore Ball Mill,Limestone Raymond Mill,Copper Ore Ball Mill Machine
henan ascend machinery , https://www.ascendminingcrusher.com