- Model NO.: H77
- Connection Form: Wafer
- Pressure: Ordinary Pressure
- Sealing Form: Gland Packings Globe Valve
- Standard: ANSI
- Size: 2" to 54"
- Certificates: API 6D, CE, ISO9001
- Delivery Detail: 20~45 Days According to The Specific Quantities
- Transport Package: Standard Export Wooden Case
- Origin: China
- Material: Cast Steel
- Structure: Swing
- Function: Ddcv Double Lobe, Nrvr Silence, Sfcv Rubber Lobe, Nrvz Silence, Nrvg Silence
- Flow Direction: Unidirection
- Application: Industrial Usage, Water Industrial Usage
- Class: 150lb to 2500lb
- Application Fields: Metallurgy,Light Industrial,Electric Power,Petroch
- Trademark: NAIBANG
- Specification: API598, API6d, ANSI, Bs, DIN, JIS
- HS Code: 8481300000
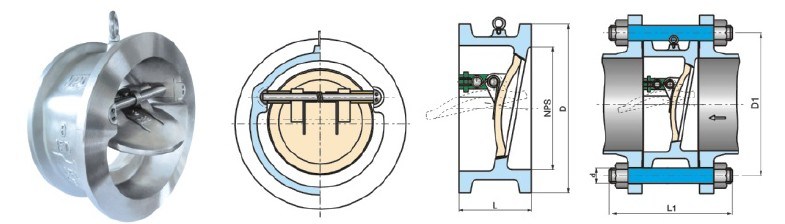
Wafer check valve is applicable for various pipelines with nominal pressure of PN1.0 Mpa~42.0Mpa, Class 150LB~2500LB and nominal diameter of DN15~1200mm,
NPS 1/2-48 and working temperature of -196~540 degree Celsius to be used for
protecting from medium backflowing.
The different materials selection can apply to the medium involving water, steam, oils, nitric acid, acetid, strong oxidizing medium and urea etc.
1)Standards:
A)Design&Manufacture: API 6D, API 594, ASME B16.34
B)Face to Face: API 594, API 6D
C)Connection End: ASME B16.5, ASME B 16.47
D)Test and Inspection: ISO5208, API 6D
2)Sizes: 2" - 40" or DN50 - DN1000
3)Pressure Rating: Class150 - Class1500 or PN16 - PN250
4)Material: WCB, LCB, WC6, WC9, C12, C5, CF8, CF3, CF3M, CF8M, etc.
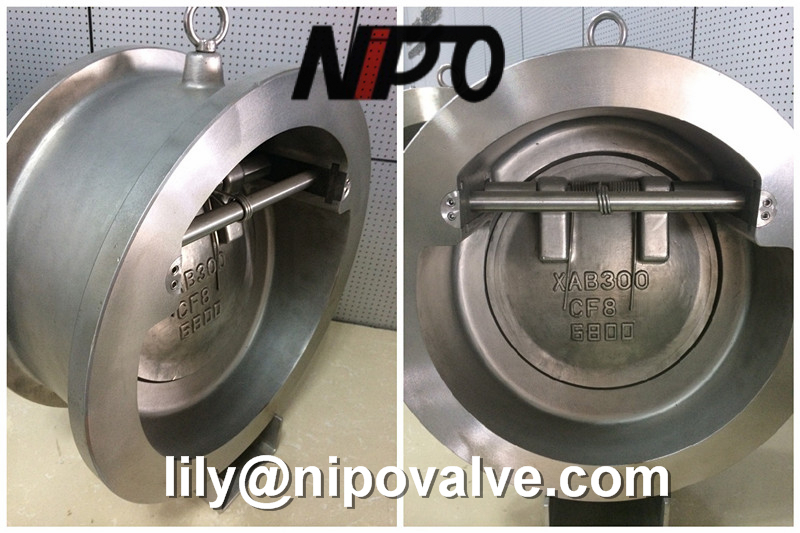
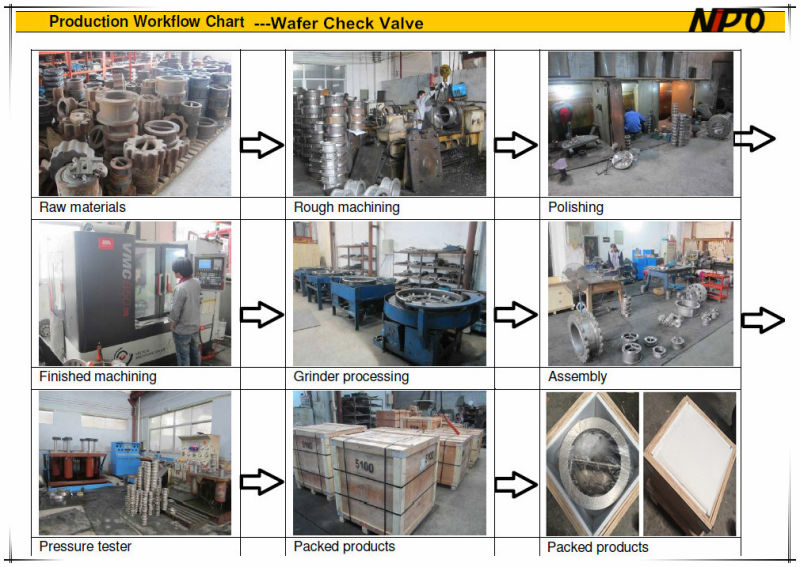
Â
Design and manufacture | API594,API 6D,JB/TB8937 |
Face to face and end to end | API594,API6D,DIN3202,JB/T8937; |
Pressure-temperature rating | ASME B16.34,DIN2410,GB/T9124,HG20625,SH3406,JB/T74 |
Inspection and test | API598,JB/T9092; |
Pipe flange | JB/T74~90,JB/T9112-9124,HG20592~20635,SH3406,ASME B16.5,DIN2543~2548,GB/T13402,API605,ASME B16.47. |
Compression molding is a manufacturing process that uses a cavity half and a core half of a mold to form material into a specific shape created by the two mold halves. Compression molds vary depending on the material being compressed and the dictates of the type of mold required.
Typically, a compression mold is mounted in a vertical press (unlike the horizontal presses that are prevalent in the Injection Molding process). Compression molding often requires that the [charge" of material be loaded into the mold, either manually or automatically, prior to the mold halves closing.
- The loss of raw materials is small and will not cause too much loss (usually 2% to 5% of the product quality).
- The shrinkage of the product is small and the repeatability is good.
- A mold with a large number of cavities can be placed on a given template, and the productivity is high.
- It can be adapted to automatic feeding and automatic removal of products.
- High production efficiency, easy to realize specialized and automated production.
- The product has high dimensional accuracy and good repeatability.
- The surface is smooth and clean without secondary modification.
- Products with complex structures can be formed at one time.
- Mass production, relatively low price.
we ever did many compression silicon parts , the hardness from 30shore A till 80shore A, colors can be customized whatever you want, we can do the compound color for you. Several free samples for the review before the overall demand running to ensure everything is clear and aligned to go. Please contact us for the professional suggestions, we have been in this field for more than 15years. thanks.
Compression Molding,Compression Forming,Rubber Compression Molding,Compression Moulding Process
Suzhou FCE precision electronics Co., LTD , https://www.fcesz.com