Guangzhou PuTian Motorcycle Parts Co.,LTD. is a professional factory with more than 10 years of experience in researching and producing brake pads for automatic transmission. PuTian features close collaboration with various vehicle manufacturers at home and aboard.The brake shoe is constituted of high-density, pure aluminum alloy by casting under 180T full automatic manipulator die-casting machine. The surface of the brake shoe goes through antiseptic treatment and sand blasting with premium stainless steel, and ends up with the high temperature passivation. The procedures improve the products' appearance and ward off fracture and slip situations while guaranteeing the pore-free and high-density internal quality.
  We always meet the needs of market consumers by sticking to our principles:depending on science&technology,pursuing top quality,striving for perfection,offering excellent service.Consumers home and abroad are warmly welcomed to contact us for cooperation and co-prosperity!
Product Description
Product Name | Motorcycle Cluth Hub |
Size | Standard size |
Packing | Box+Bag packing |
Quality | Top Quality |
Sample | Offer |
Main Market | South American. Afrian .Middle East |
Payment term | 30% deposit and pay balance after all goods ready |
We supply All kinds of Motorcycle Brake shoe
Factory direct, quality assurance, best price
Accept trial order
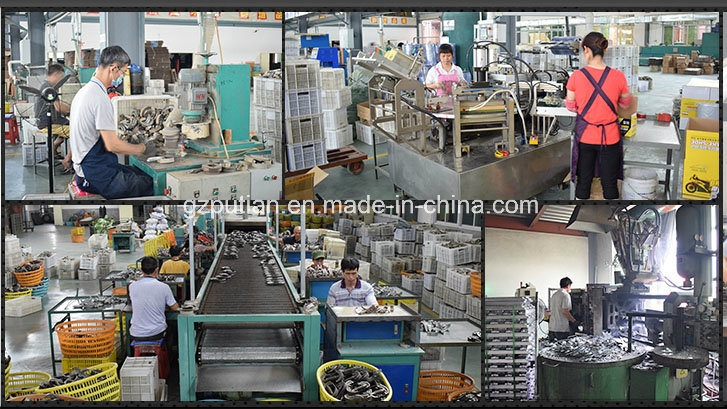
Contact us
Contact: Laila Liu
 Mobile : +86 18102717080
Tel: +86 20-81331079
Â
Sand casting is used to produce a wide variety of metal components with complex geometries. These parts can vary greatly in size and weight, ranging from a couple ounces to several tons. Some smaller sand cast parts include components as gears, pulleys, crankshafts, connecting rods, and propellers. Larger applications include housings for large equipment and heavy machine bases. Sand casting is also common in producing automobile components, such as engine blocks, engine manifolds, cylinder heads, and transmission cases.
Sand casting, the most widely used casting process, utilizes expendable sand molds to form complex metal parts that can be made of nearly any alloy. Because the sand mold must be destroyed in order to remove the part, called the casting, sand casting typically has a low production rate. The sand casting process involves the use of a furnace, metal, pattern, and sand mold. The metal is melted in the furnace and then ladled and poured into the cavity of the sand mold, which is formed by the pattern. The sand mold separates along a parting line and the solidified casting can be removed. The steps in this process are described in greater detail in the next section. In sand casting, the primary piece of equipment is the mold, which contains several components. The mold is divided into two halves - the cope (upper half) and the drag (bottom half), which meet along a parting line. Both mold halves are contained inside a box, called a flask, which itself is divided along this parting line. The mold cavity is formed by packing sand around the pattern in each half of the flask. The sand can be packed by hand, but machines that use pressure or impact ensure even packing of the sand and require far less time, thus increasing the production rate. After the sand has been packed and the pattern is removed, a cavity will remain that forms the external shape of the casting. Some internal surfaces of the casting may be formed by cores.
Sand casting is able to use of almost any alloy. An advantage of sand casting is the ability to cast materials with high melting temperatures, including steel, nickel, and titanium. The four most common materials that are used in sand casting are shown below, along with their melting temperatures
Materials Melting temperature
Aluminum alloys 1220 °F (660 °C)
Brass alloys 1980 °F (1082 °C)
Cast iron 1990-2300 °F (1088-1260 °C)
Cast steel 2500 °F (1371 °C)
The material cost for sand casting includes the cost of the metal, melting the metal, the mold sand, and the core sand. The cost of the metal is determined by the weight of the part, calculated from part volume and material density, as well the unit price of the material. The melting cost will also be greater for a larger part weight and is influenced by the material, as some materials are more costly to melt. However, the melting cost in typically insignificant compared to the metal cost. The amount of mold sand that is used, and hence the cost, is also proportional to the weight of the part. Lastly, the cost of the core sand is determined by the quantity and size of the cores used to cast the part.
Sand casting process advantages
Can produce very large parts
Can form complex shapes
Many material options
Low tooling and equipment cost
Scrap can be recycled
Short lead time possible
Applications:
Construction Machine Parts,Scaffolding Parts,Engine blocks and manifolds, machine bases, gears, pulleys, agriculture parts,Marine Parts,medical parts,hardware, automobile parts,ect.
Sand Casting,Aluminum Sand Casting,Stainless Steel Sand Casting,Sand Precision Casting
Ningbo City Yinzhou Ruican Machinery Co.,Ltd , https://www.ruicanmanufacturer.com